Among the many maxims Benjamin Franklin gave to the business world, the most famous might be, “If you fail to plan, you are planning to fail.” Strategic planning is a critical skill for today’s business leaders, regardless of their field. Planning provides the roadmap for a business, giving managers and everyone else clarity on goals and how they can be achieved.
In the manufacturing sector, planning is especially important because manufacturing involves complex processes and long lead times. Plans must consider the interaction of a wide network of suppliers and distributors as well as the impact of changing customer demands.
Recent developments in the manufacturing space have made planning even more complex. The following are some of the top challenges manufacturing is facing in today’s business landscape, along with some thoughts on how leaders can plan to address them.
Meeting Demands for Greater Sustainability
Consumers are more concerned than ever about sustainability. Recent studies suggest the market is approaching a tipping point, at which a commitment to sustainability will become table stakes for companies seeking to attract and retain customers. Those who can show they are acting in an environmentally responsible way will have a strong competitive advantage.
For manufacturing companies, this trend requires finding a way to reduce waste, pollution, and energy consumption while still delivering quality products at reasonable prices. Management must find ways to drive sustainability without compromising efficiency.
It is often a combination of hundreds of small changes that lead to great results. One small example is shifting to lithium-ion power to boost both sustainability and efficiency in manufacturing. Lithium-ion batteries offer faster charging capabilities and higher energy density when compared with traditional lead-acid batteries, giving companies greater efficiency and reliability. At the same time, lithium-ion boosts sustainability by delivering a longer lifespan that reduces waste.
Addressing the Growing Skills Gap
The growing skills gap in the manufacturing space is profoundly impacting leaders, with over 80 percent citing it as their top challenge in a recent survey. Experts project that, by the end of the decade, manufacturing in the US could be facing a 2.1 million job shortage brought about by an aging workforce and a shift in worker preferences. In Canada, where our company is based, there is a current shortage of 200,000 manufacturing workers, which is expected to grow to 600,000 by 2030.
Investing in workforce development programs is one way companies can decrease the gap. Internal training programs that teach the skills needed to utilize emerging technologies can help in this area. Companies can also consider partnering with educational institutions like community colleges, technical colleges, and vocational training programs that provide training in the types of skills needed in manufacturing.
Building a positive work environment is also critical for attracting the workers needed to support manufacturing operations, which is why leadership must prioritize competitive wages and benefits to attract quality workers. The skills gap makes this even more important, as it increases competition and makes retaining employees more challenging. Providing clear career paths and opportunities for promotion are also critical factors in building and sustaining positive work environments.
Managing Technological Advancements
Advances in technology have brought considerable opportunities to the manufacturing sector. From telematics to augmented reality to operator-asset technology, leaders now have a number of new tools they can implement to achieve higher levels of efficiency. The challenge faced by management teams is determining which tools will actually deliver greater productivity and profitability.
For example, mobile apps have become a common tech tool for businesses seeking to streamline connections with consumers, but a company-centric app becomes just one more interface consumers need to manage in the manufacturing space. A more effective tech tool is a data interface that allows customers to link their internal resource management systems directly to a manufacturer’s client interface. The most effective technology will streamline touch points with customers rather than adding additional steps.
To thrive, manufacturing companies must plan to meet both consumer and employee expectations. In today’s business world, that means answering the call for increased sustainability, effectively addressing the skills gap, and ensuring tech tools deliver enhanced quality and efficiency. Companies that manage those challenges will stand out as the best option in the manufacturing space.
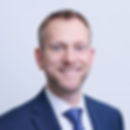
Iggy Domagalski is President & CEO of Wajax, one of Canada’s longest-standing and most diversified industrial products and services companies. He is a people-first leader with a track record of building businesses and shareholder value. With a diverse background spanning industrial equipment, finance, and acquisitions, he has led organizations of all sizes, including national publicly traded, mid-market private, small business, and non-profit. He has been named one of Canada’s Top 40 Under 40 and one of Canada’s 50 Most Inspirational Entrepreneurs.